Industrial Roof Replacement
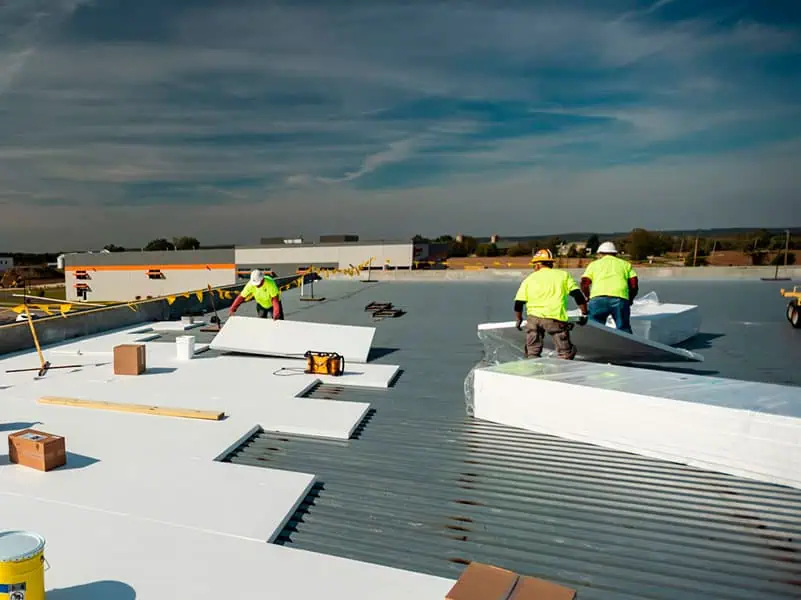
Introduction
Industrial roof replacement is a significant undertaking that involves removing and replacing the existing roof of an industrial building. This process is essential for maintaining the structural integrity, safety, and efficiency of the facility. The cost, materials, and methods used in industrial roof replacement can vary widely based on several factors.
Factors Influencing Cost
- Roof Size and Complexity
- Roofing Material
- Accessibility
- Labor Costs
- Additional Costs
Common Roofing Materials
- EPDM (Ethylene Propylene Diene Monomer)
- TPO (Thermoplastic Polyolefin)
- Metal Roofing
- Modified Bitumen
- PVC (Polyvinyl Chloride)
Replacement Process
- Assessment and Planning
- Preparation
- Installation
- Finishing Touches
- Final Inspection
Cost Estimates
- Average cost ranges from $5 to $15 per square foot. For example, replacing a 10,000 square foot flat roof could cost between $50,000 and $150,000.
Methods to Reduce Costs
- Proactive maintenance and regular inspections to identify and address minor issues before they escalate.
- Timely repairs to prevent minor issues from escalating.
- Investing in high-quality materials and experienced contractors to ensure long-term durability and reduce the need for frequent repairs.
Conclusion
Industrial roof replacement is a critical investment for maintaining the safety, efficiency, and longevity of industrial buildings. Understanding the factors influencing costs, the materials available, and the replacement process can help building owners make informed decisions and ensure successful project completion. Consulting with reputable roofing professionals is recommended for accurate estimates and expert guidance.